Advanced Cleaning Robot for EasyX
Fish farming is a form of aquaculture and an important industry in Norway. Traditionally the farms are located in the sea where the fish are held in special mesh enclosures. But for the first part of the lifecycle the fish are grown in land-based facilities.


To produce healthy meat with high quality and to comply with regulations, the land-based fish tanks must be cleaned regularly. Every 12 weeks the tanks must be emptied and thoroughly cleaned and sterilized. Today this is a time consuming (1 tank/day) manual labor job made by 2 persons. This is a costly procedure where the facility must shut down its normal operation during the cleaning process.


Growing industry
In addition, fully land-based fish farming is a growing industry and with it the need to effectively also clean the tanks in these facilities. xAQ is a robot developed to do the cleaning job in a much more effective way with fewer people involved. The robot can run on vertical and extremely slippery surfaces and the operator can stay on the ground without having to rig safety equipment and scaffolding.


The robot can be operated by 1 person, and it can clean an entire tank in just 90 minutes. This largely reduces the facility downtime and therefore present a huge cost saving for the industry. In addition, it also gives a much less hazardous work environment for the cleaning personal. The xAQ robot is a result of the collaboration between Eker Design and EasyX AS. EasyX is a startup company based in Bergen Norway. The company was founded in 2020 and they tested their first POC model in may 2022.
In early 2023 EasyX contacted Eker Design to help with further design and development of the concept towards an industrialized and commercial product. After the first POC tests in 2022 there were several challenges that needed to be met.
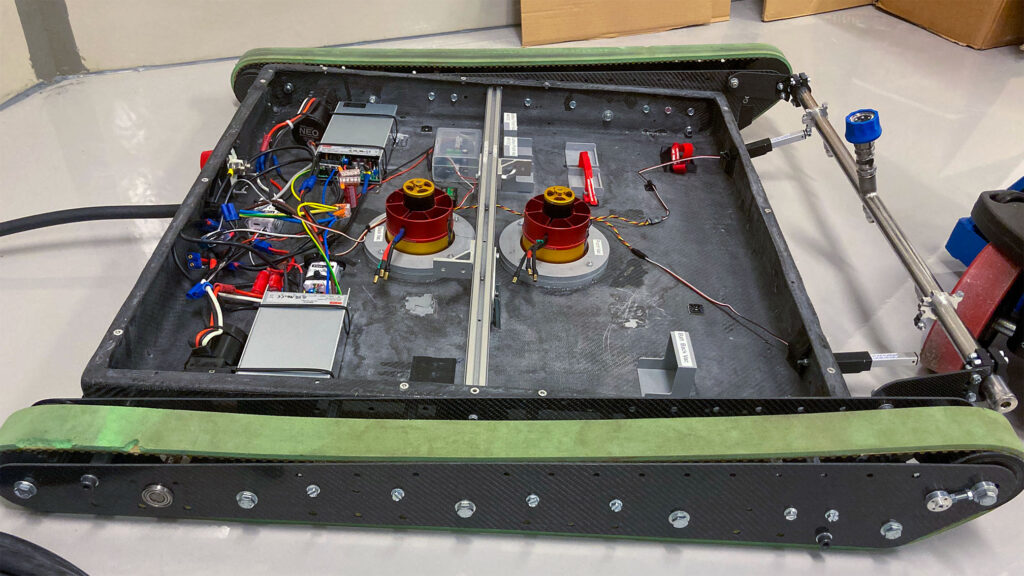
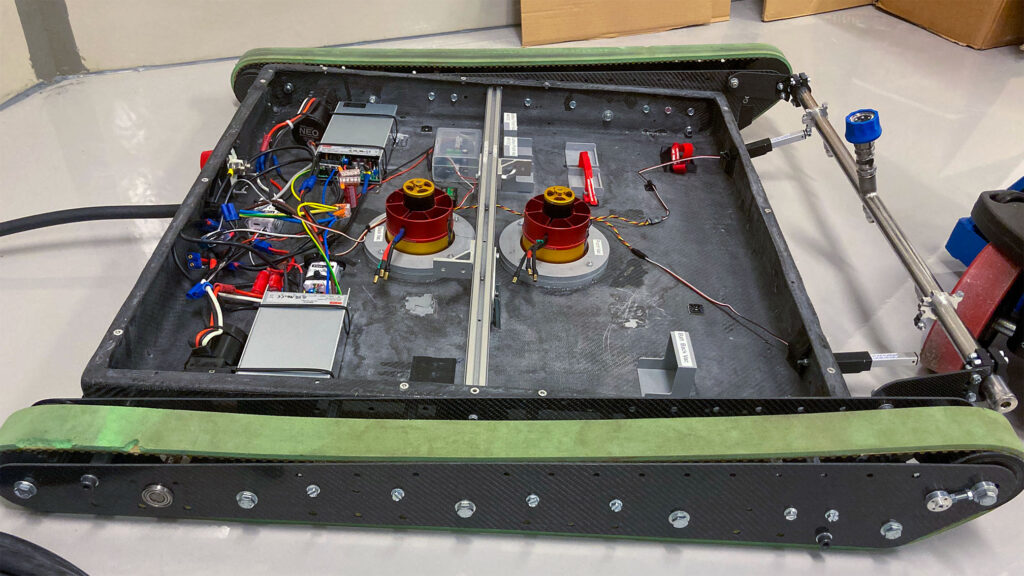
Overcoming gravity
In the fish tanks algae and other micro-organism grow on the tank walls and create an extremely slippery surface. With powerful fans xAQ creates a vacuum under its hull to securely keep itself on the vertical walls. Two motorized timing belts offer propulsion and steering. The right material and design for the vacuum gasket and the timing belts are crucial. The gasket must glide effortless on the surface and the vacuum force together with the friction of the timing belts must overcome gravity. Calculations were made early in the process to find this equilibrium.
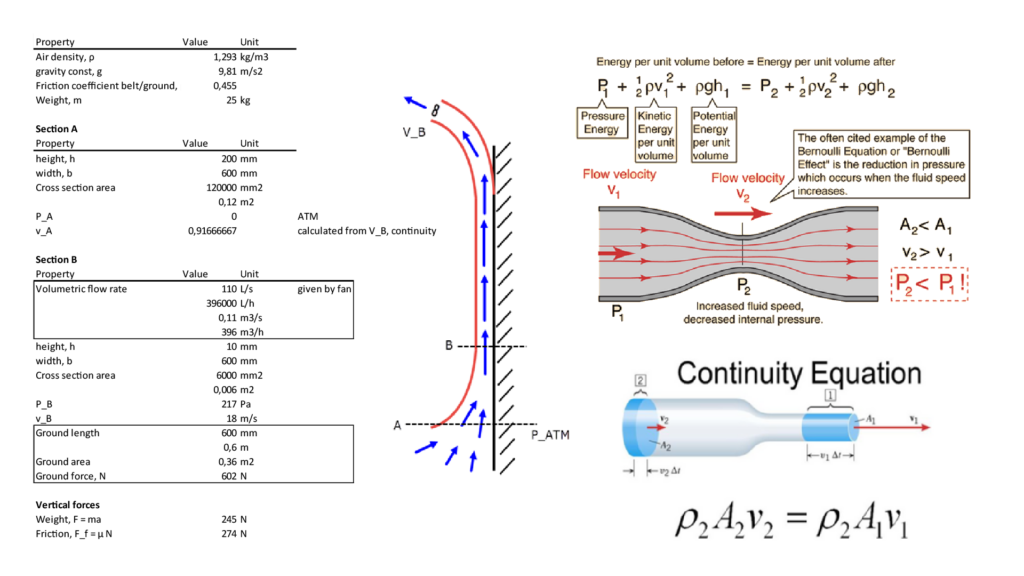
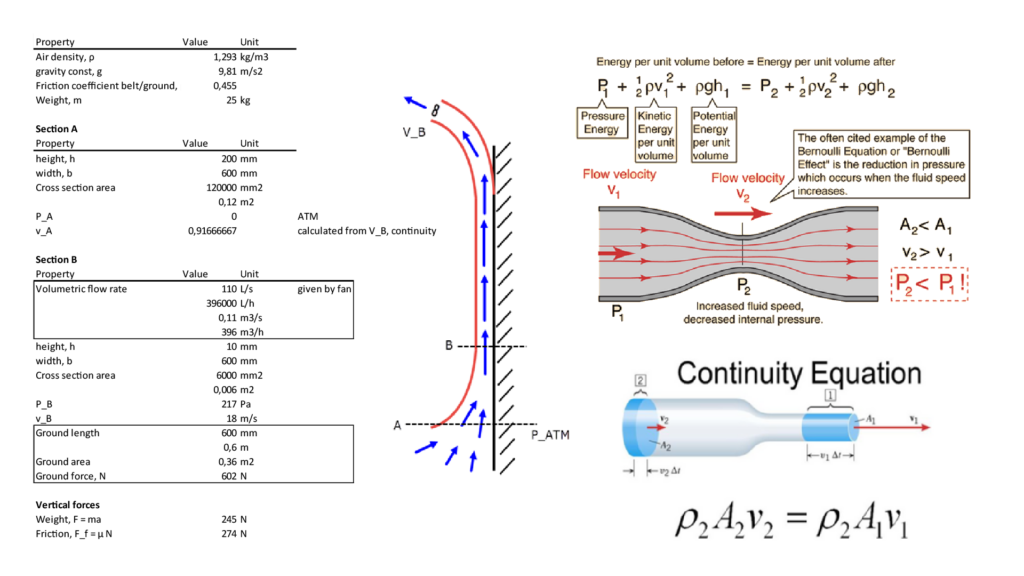
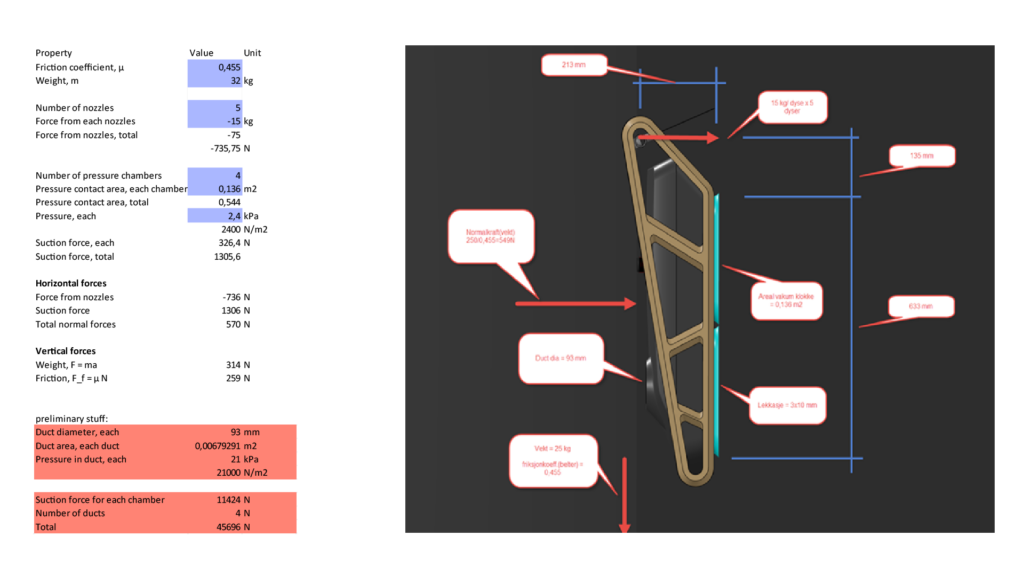
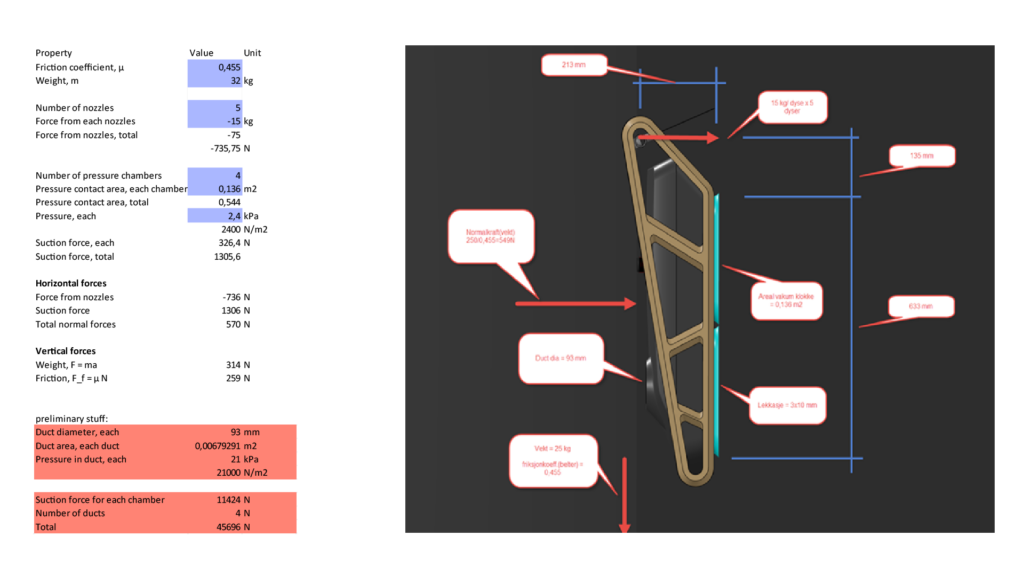
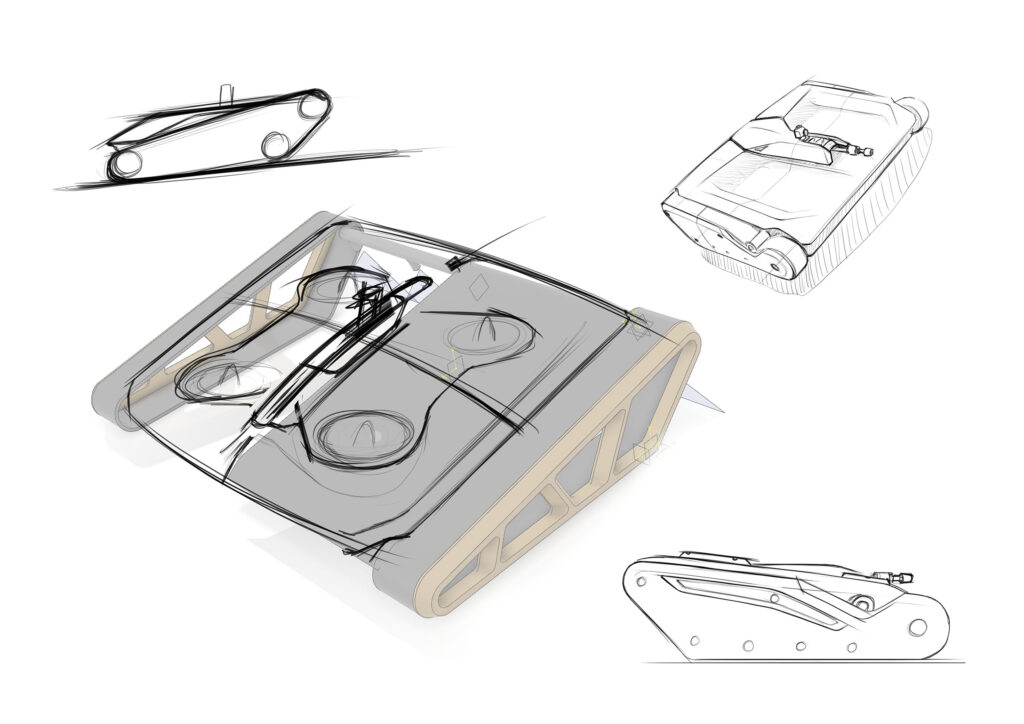
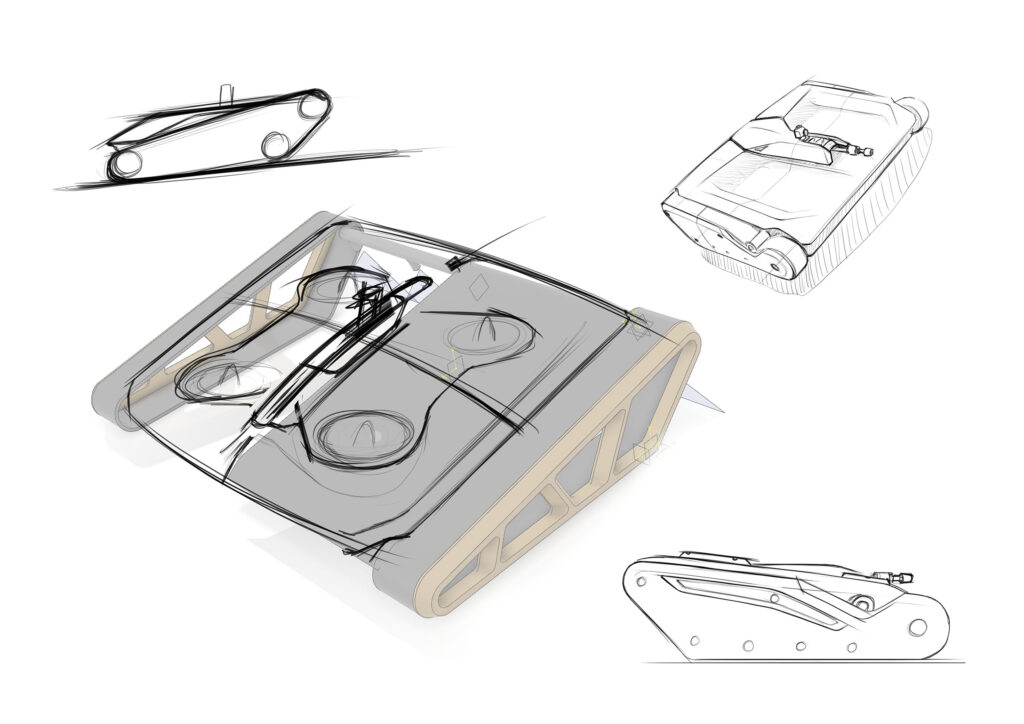
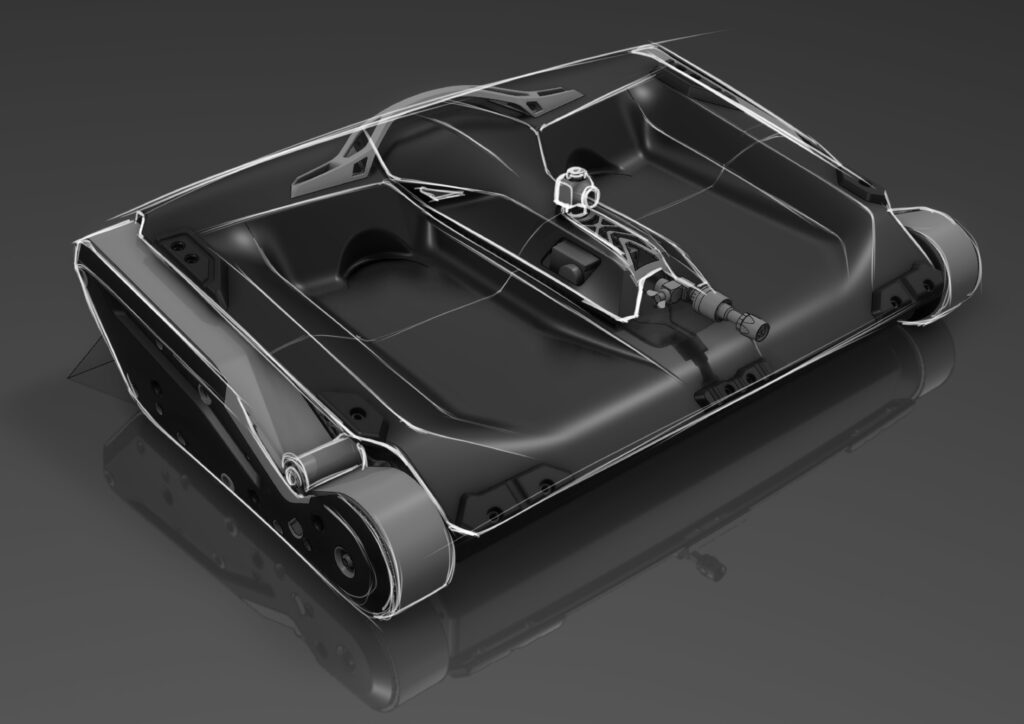
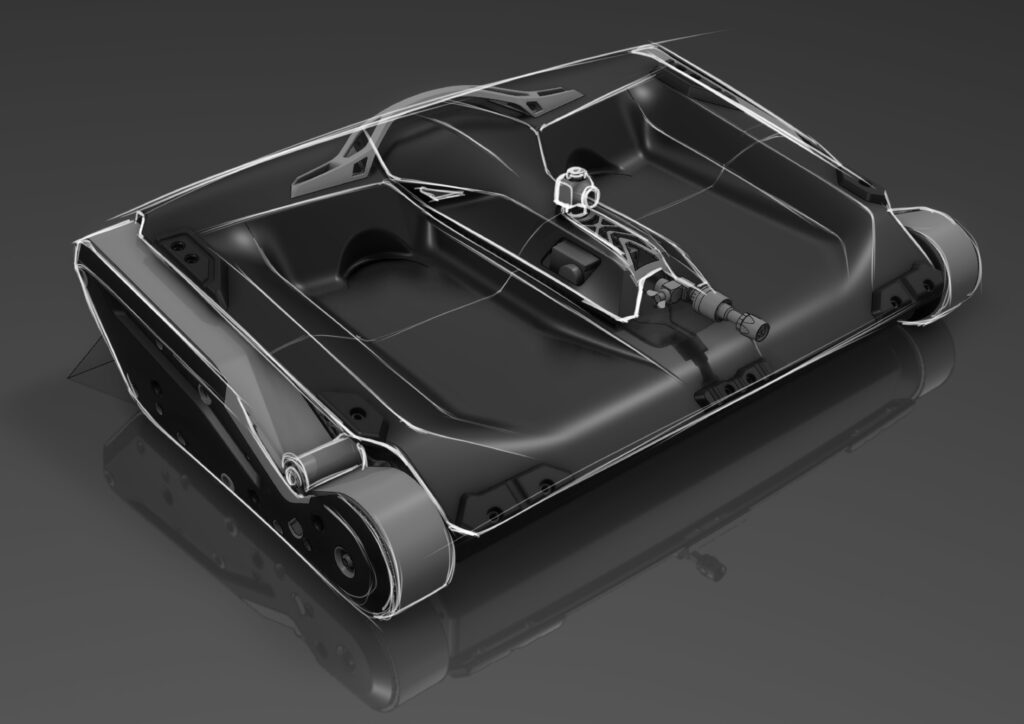
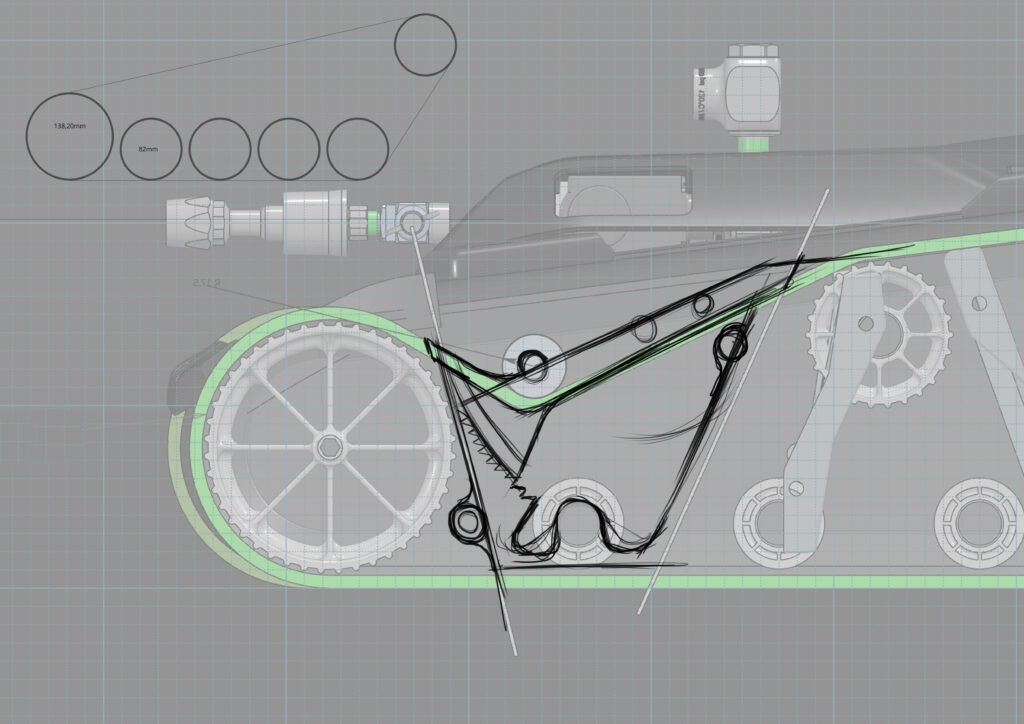
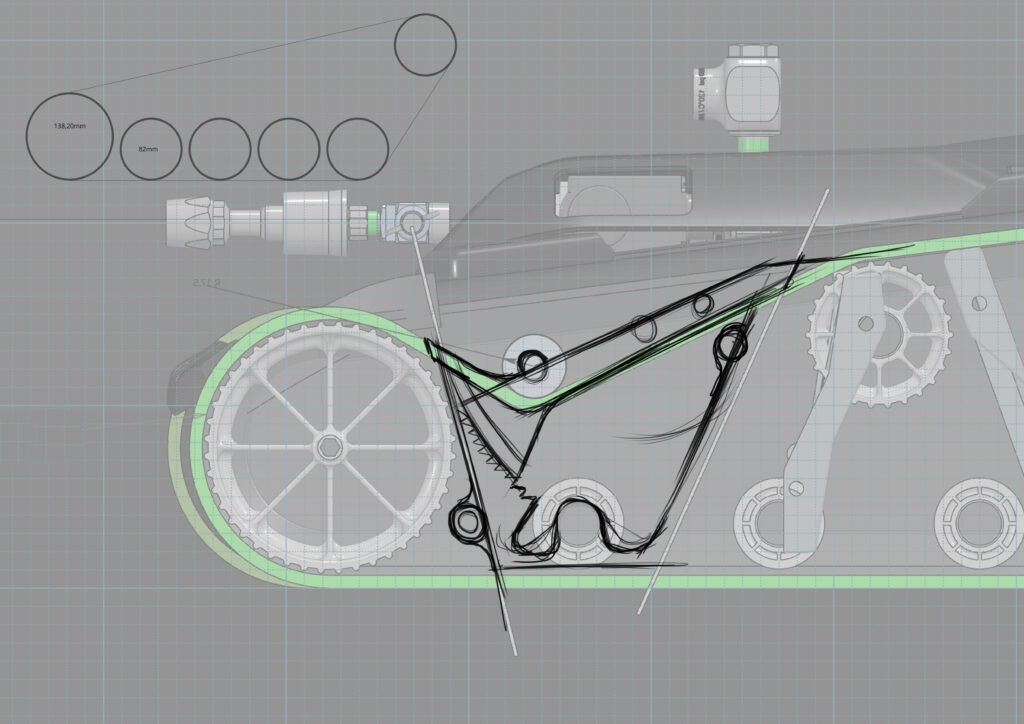
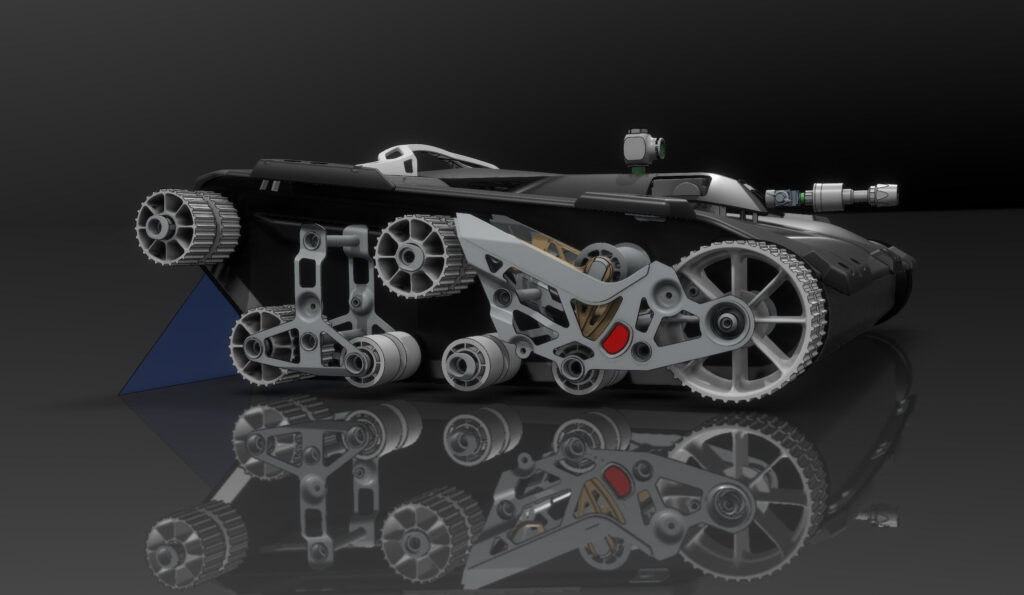
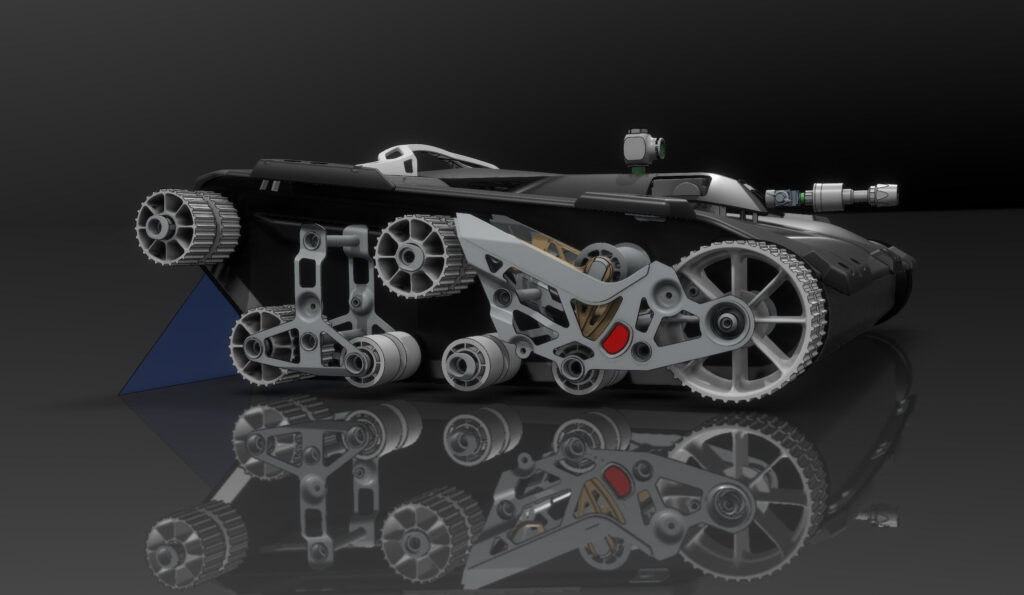
Carbon & 3D printed stainless steel
The environment in which the robot operates is both acidic and severely basic. So, all materials used needed to withstand this. Also, weight needed to be held as low as possible. To create a strong, light and corrosion resistant robot, xAQ is completely made of carbon fiber hull parts in union with 3D printed stainless steel parts. 3D printing allows for weight effective metal parts design that is still strong enough.
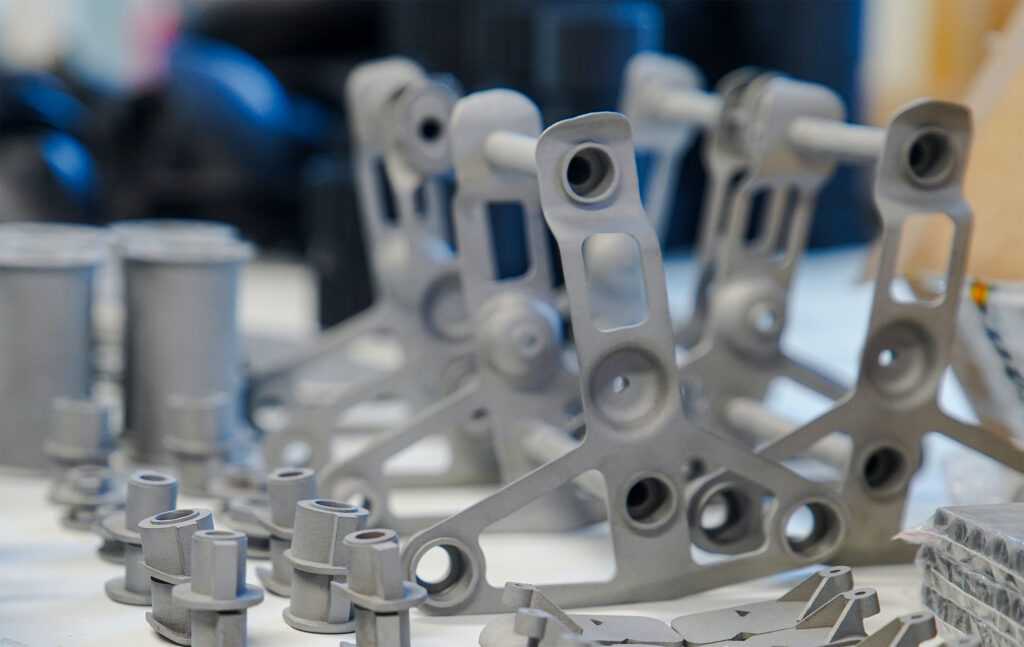
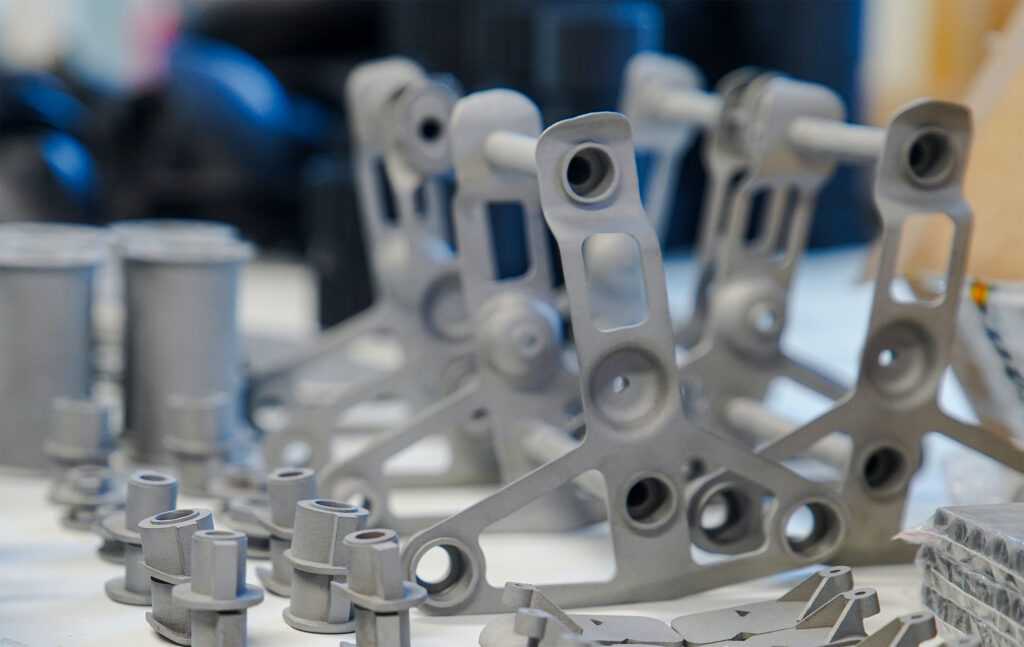
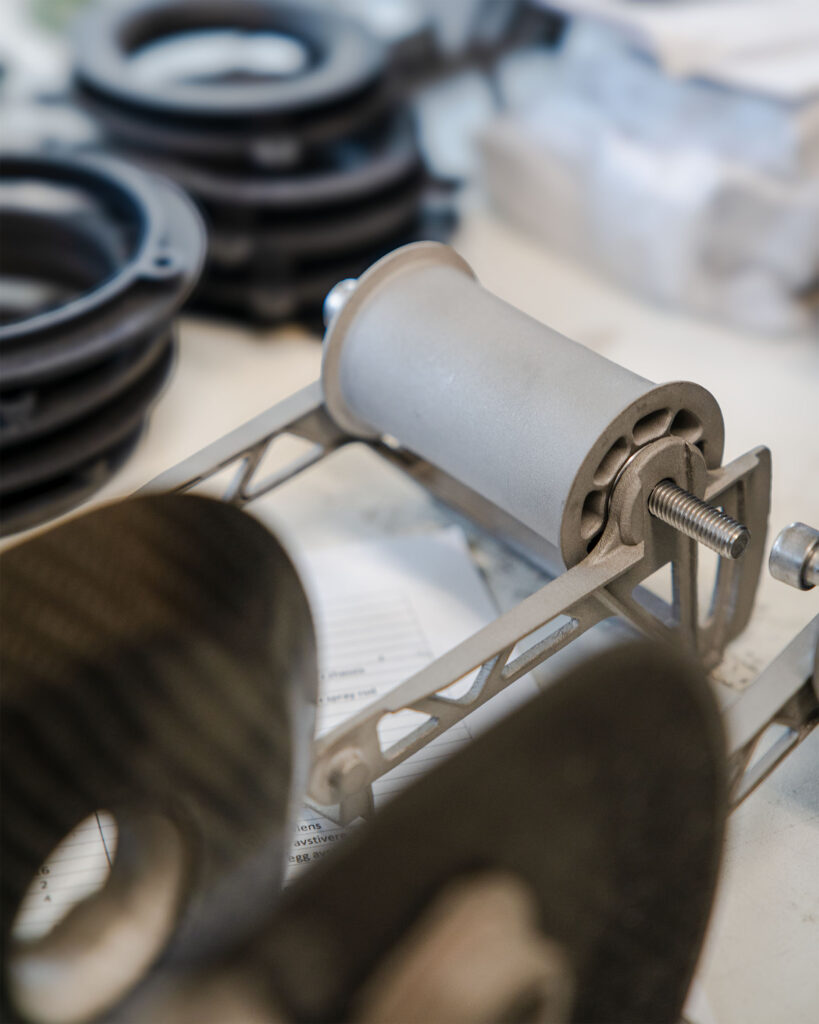
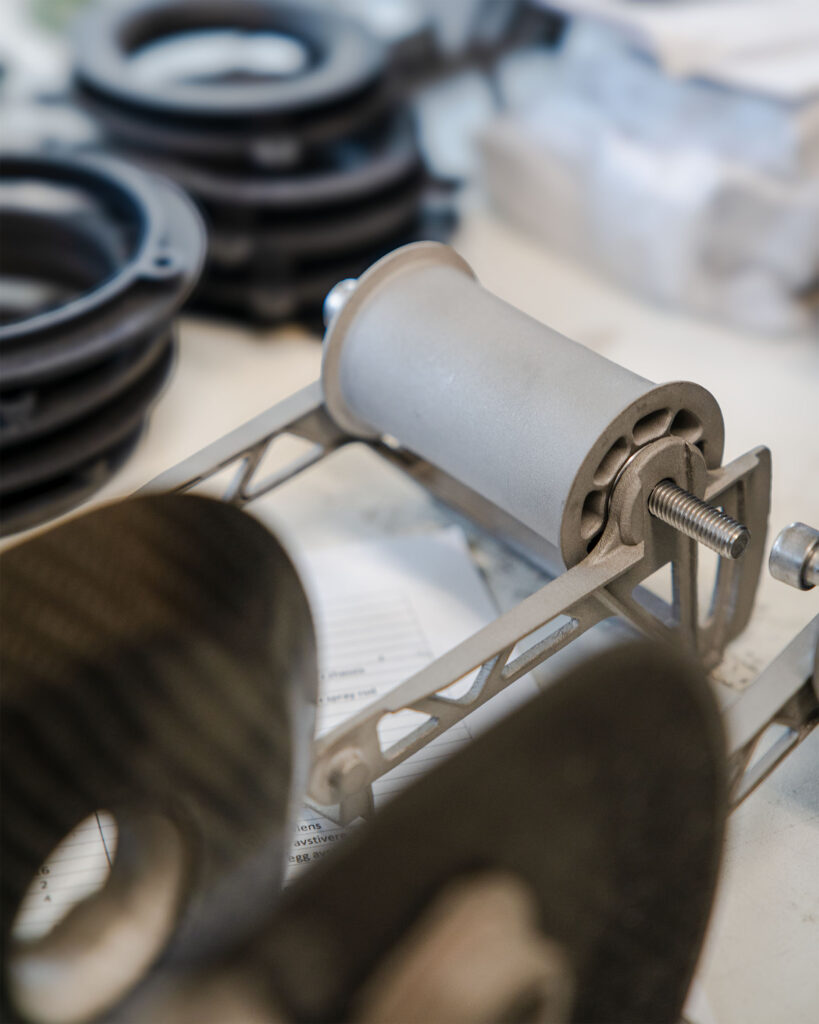
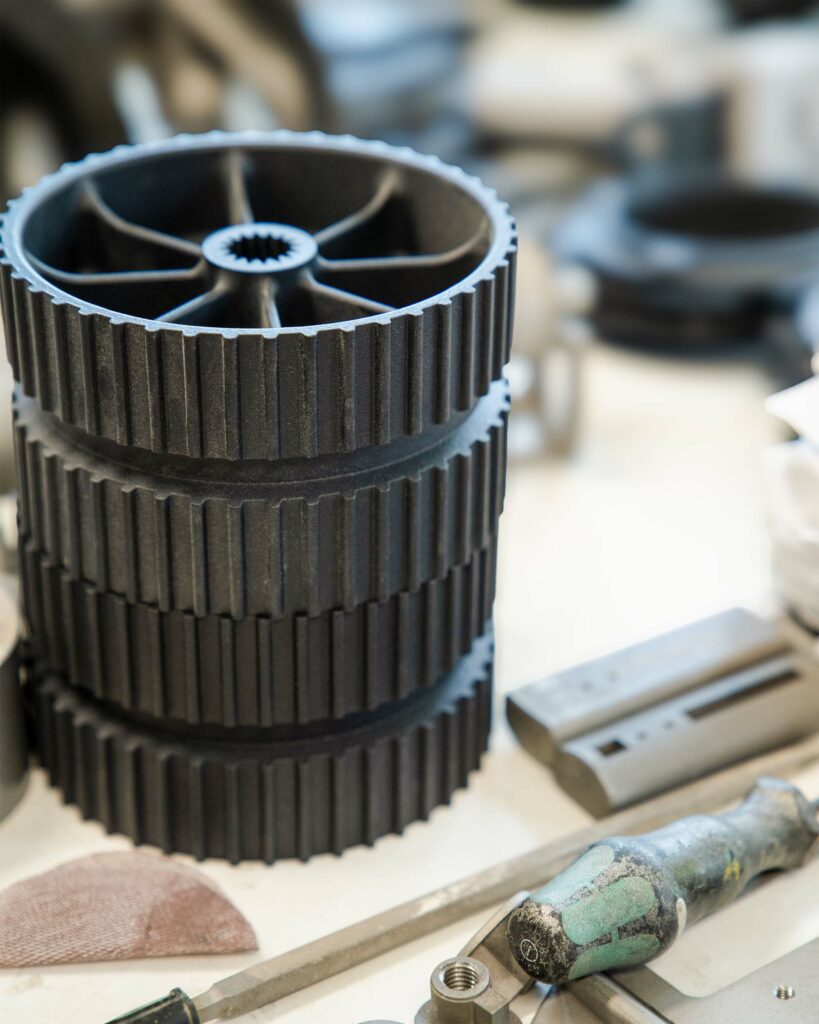
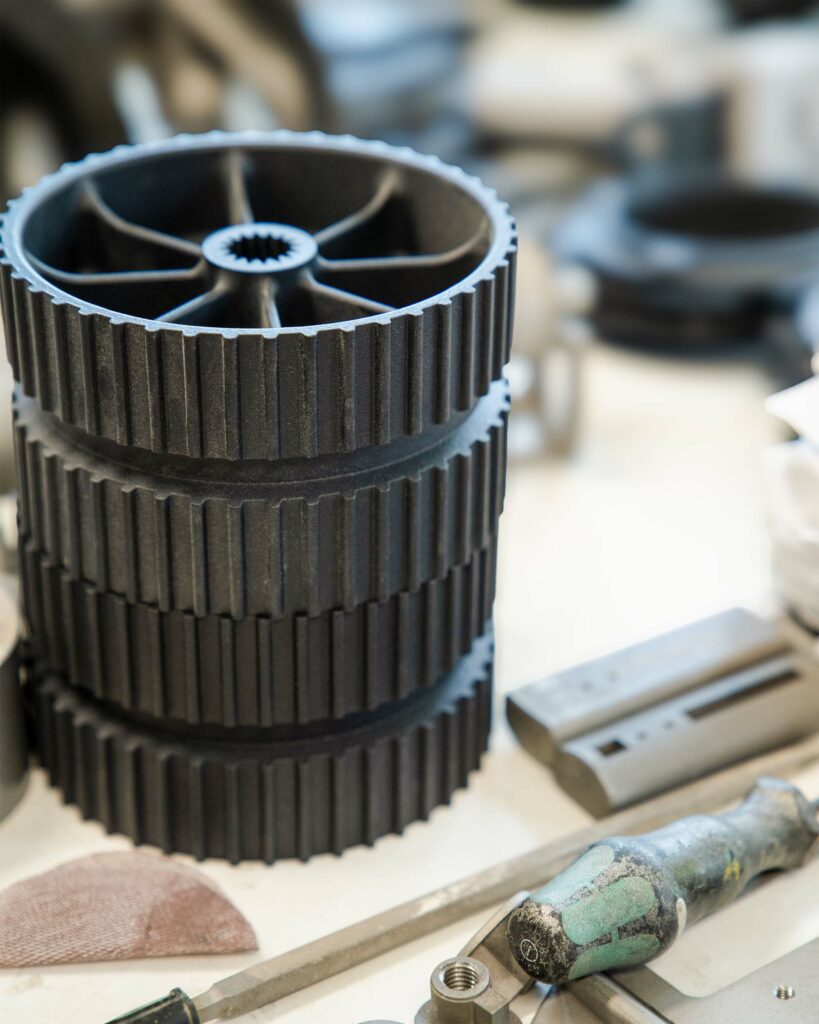
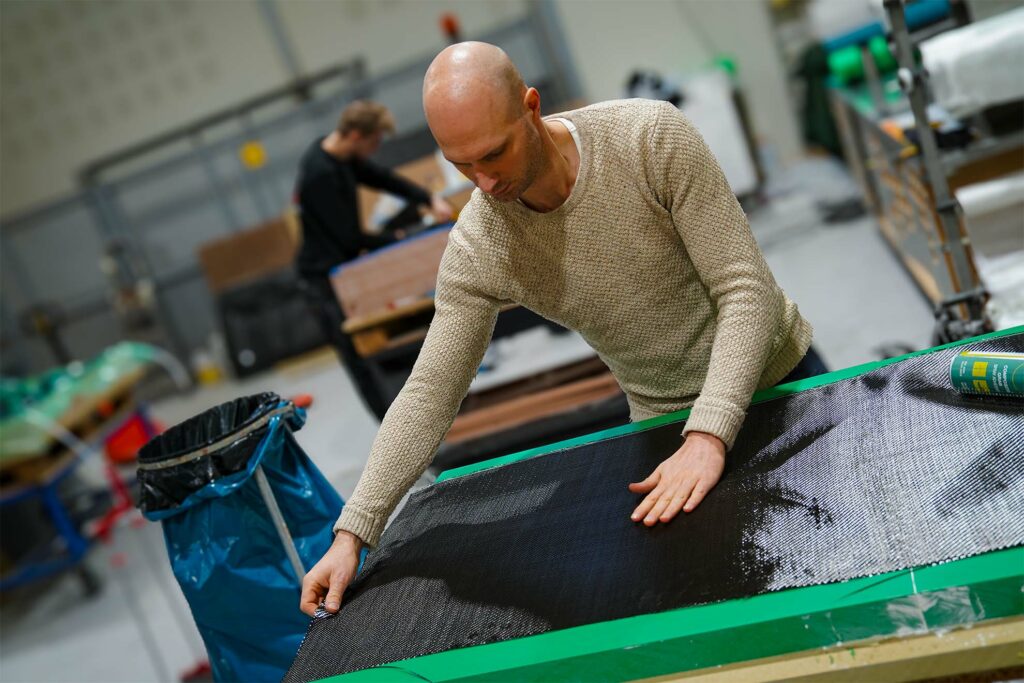
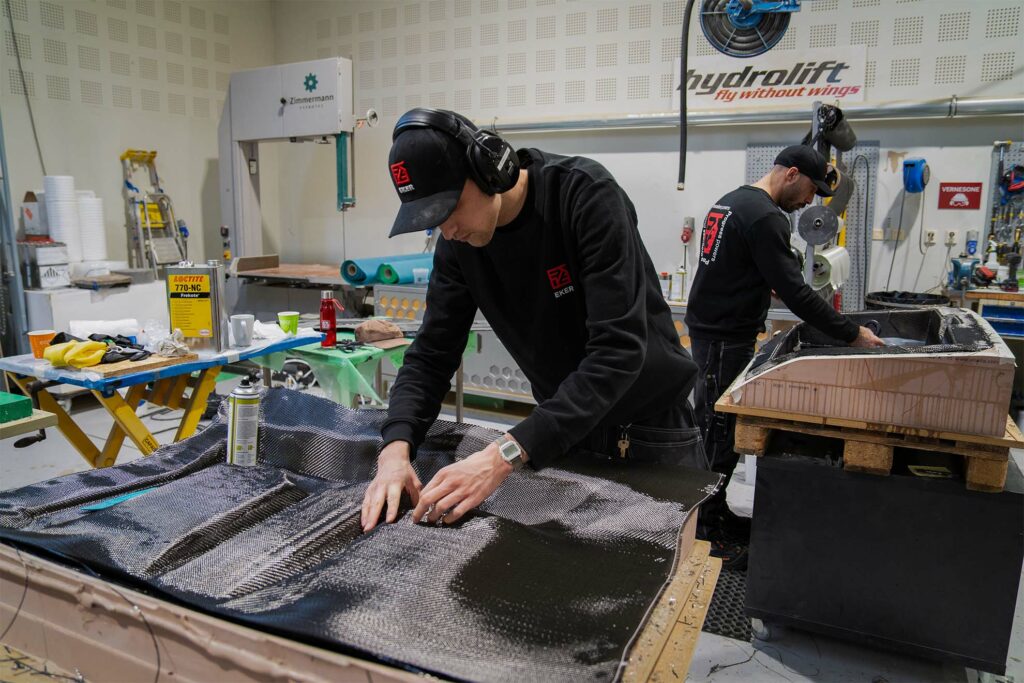
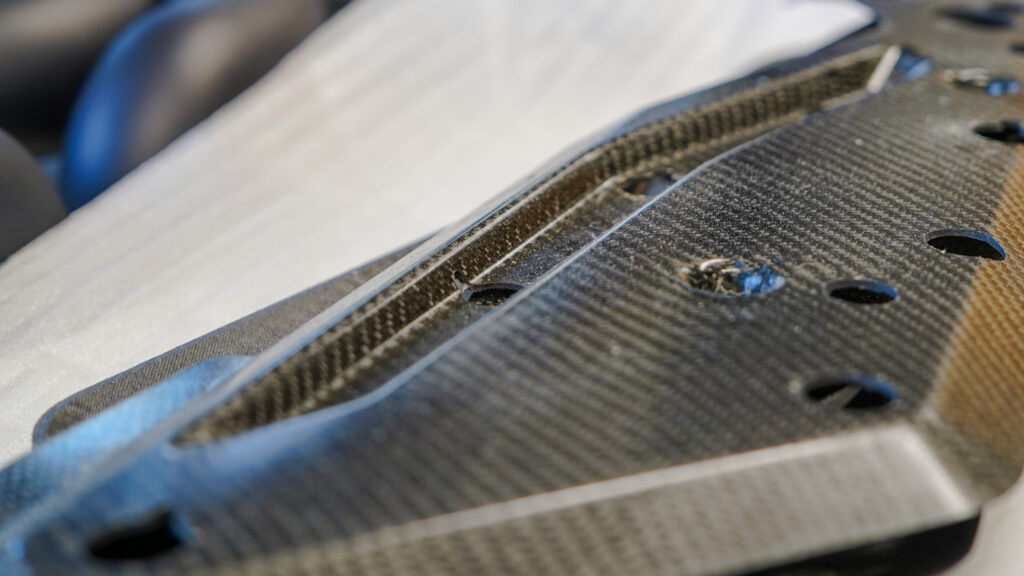
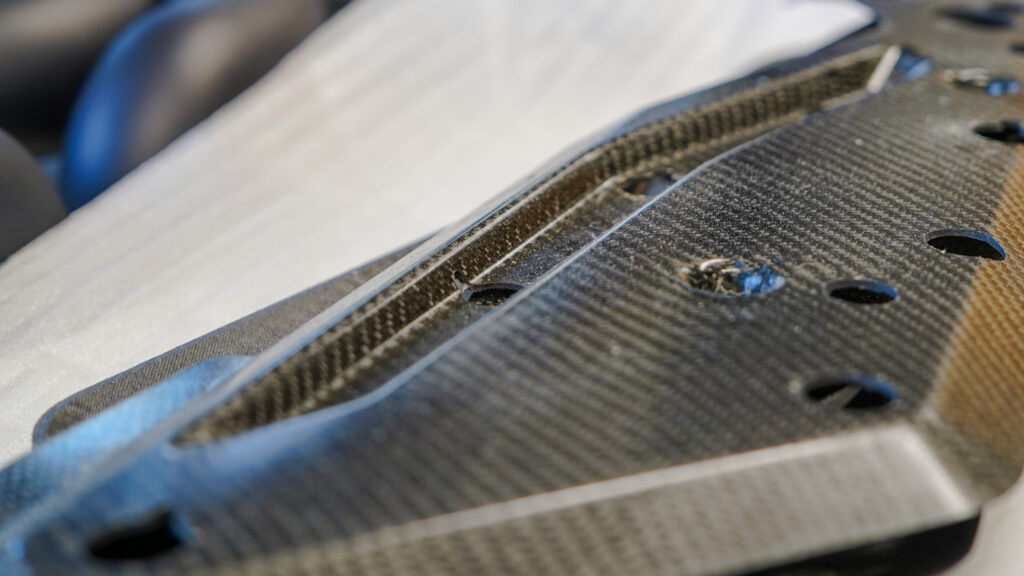
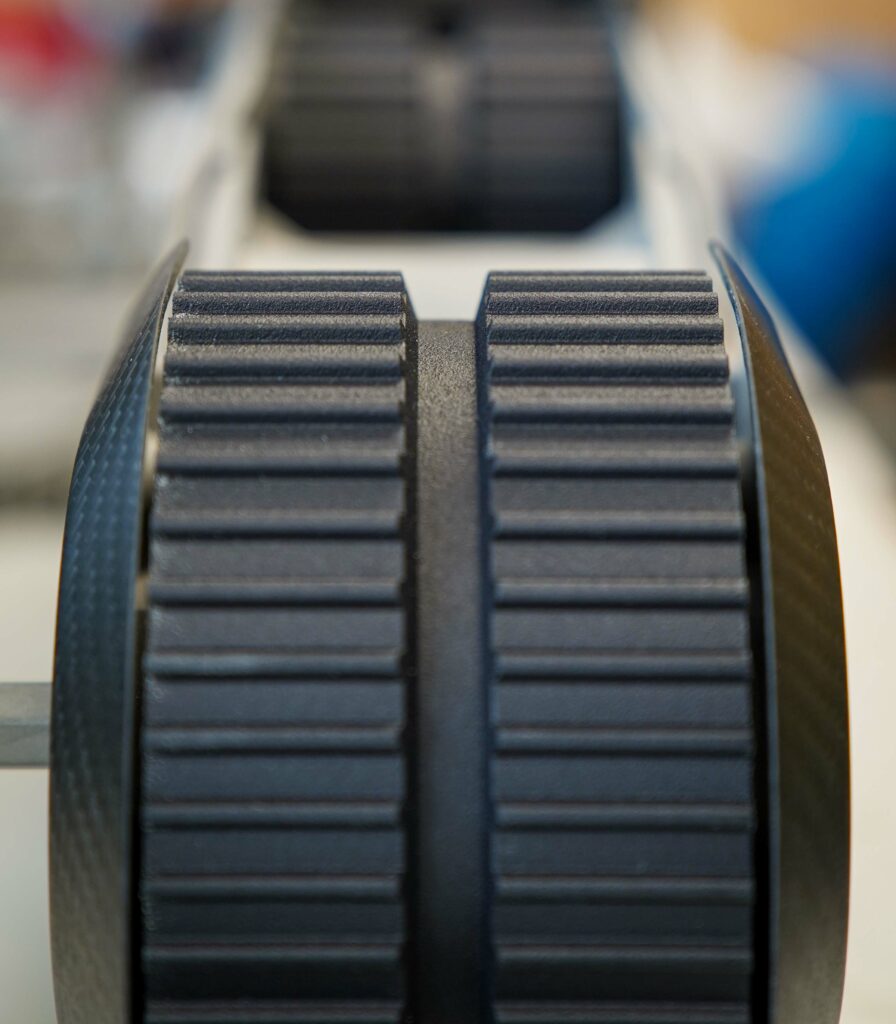
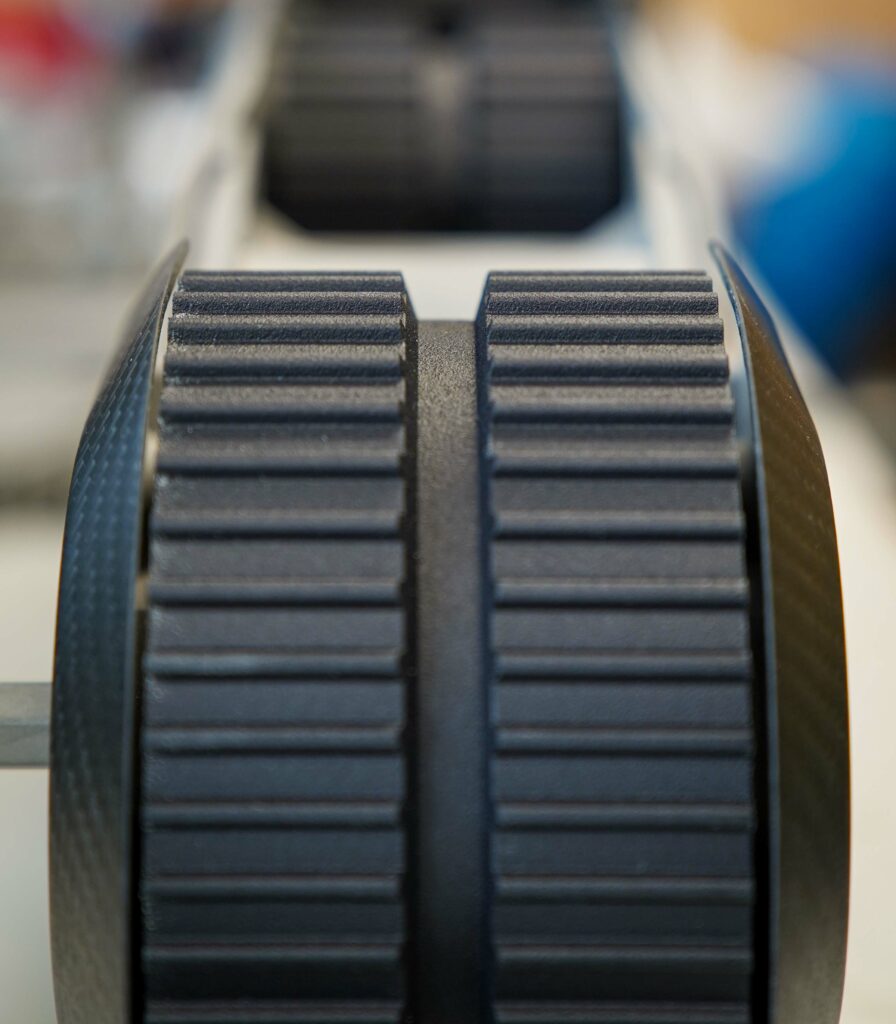
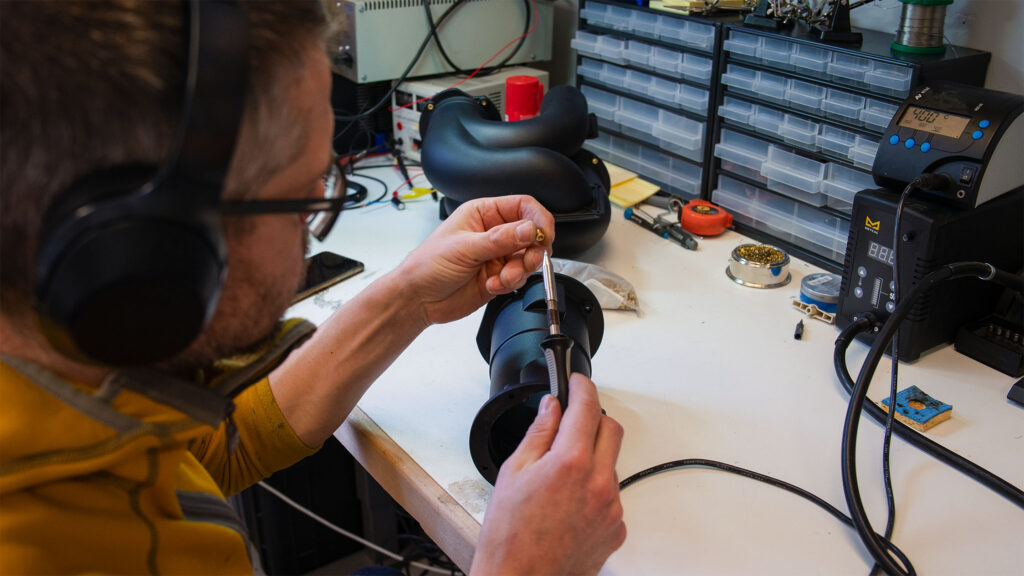
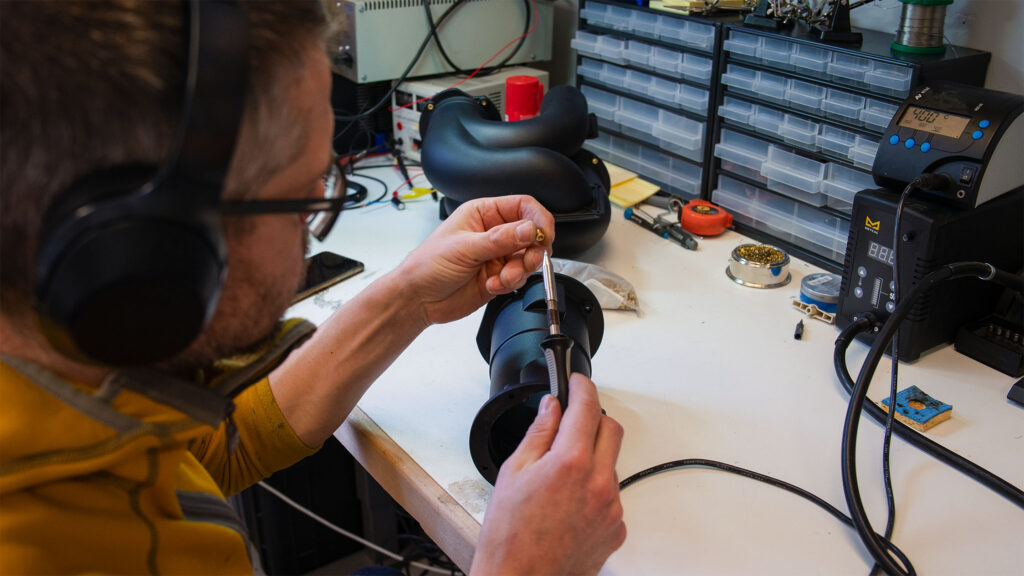
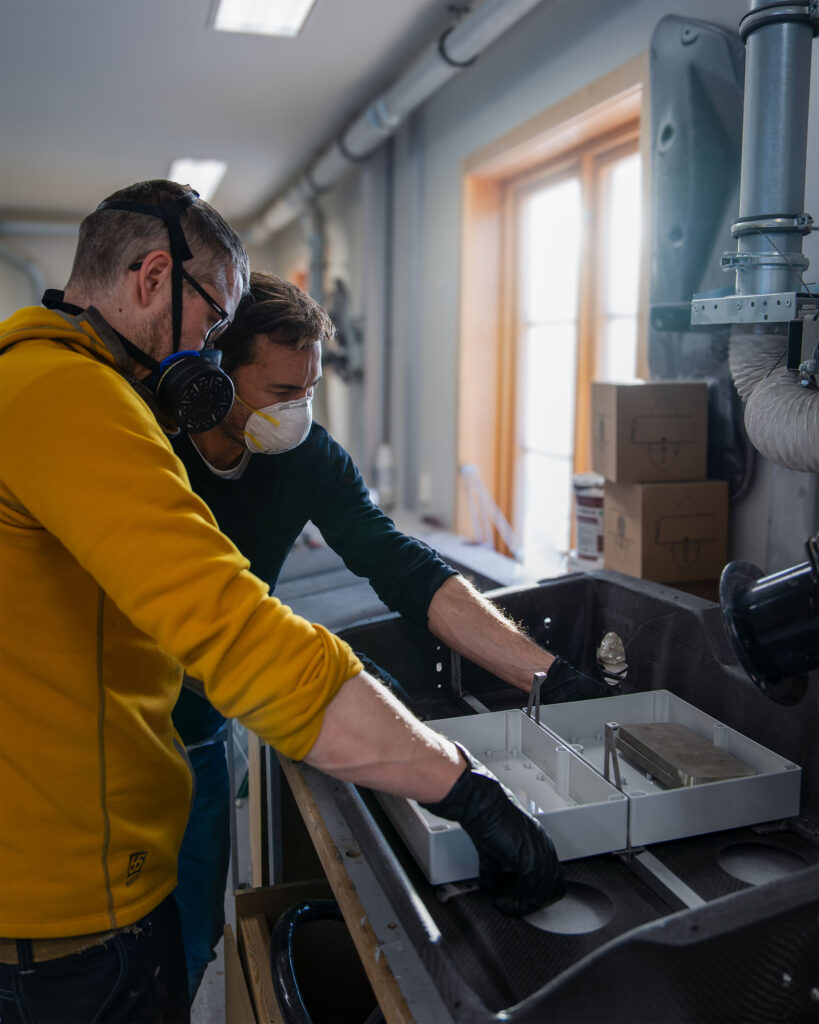
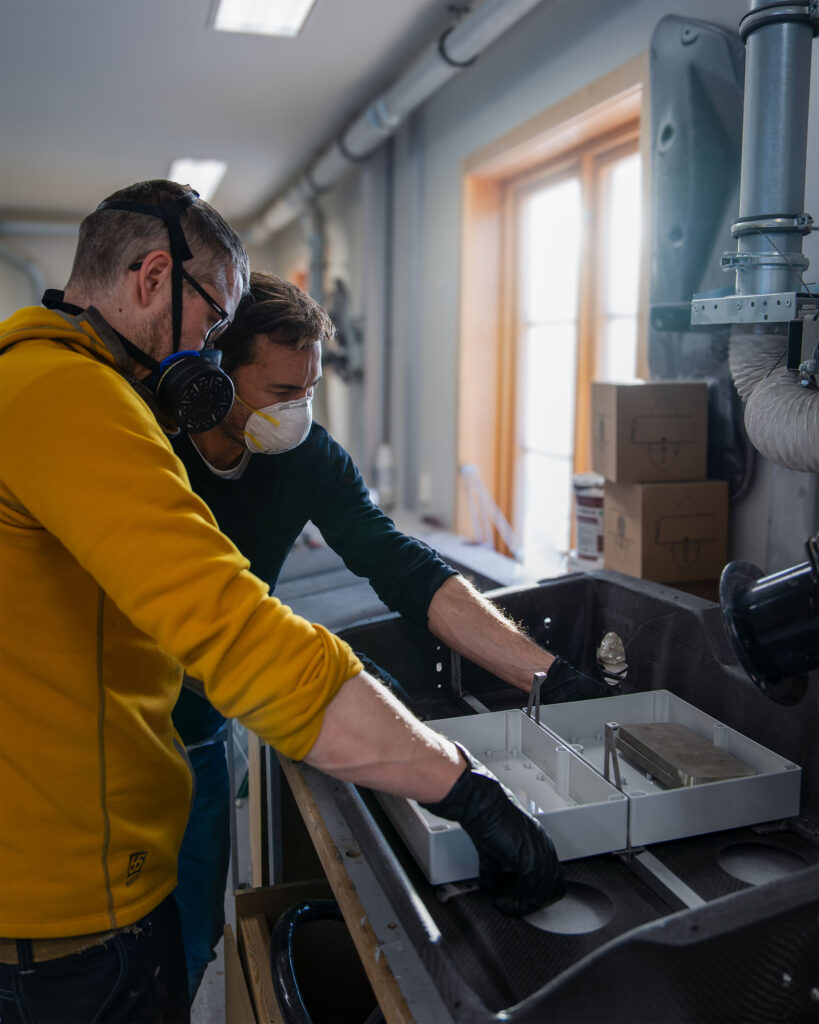
Prototype 1
In August 2023 Eker Design delivered a fully functional prototype to be used for exhibitions and further testing. After testing done by EasyX during October 2023 a few more challenges became clear, and Eker Design were again contacted to help with further development.
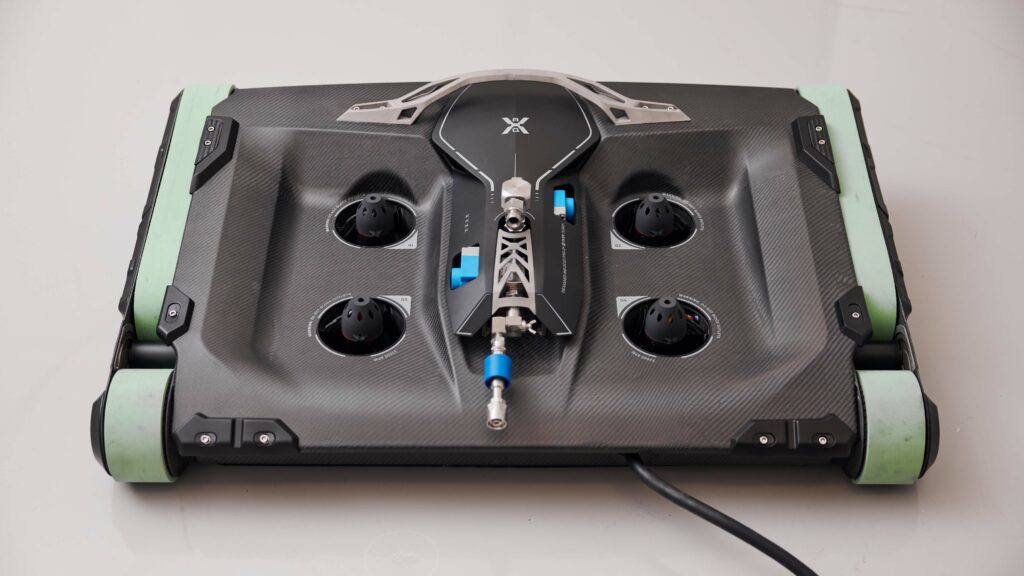
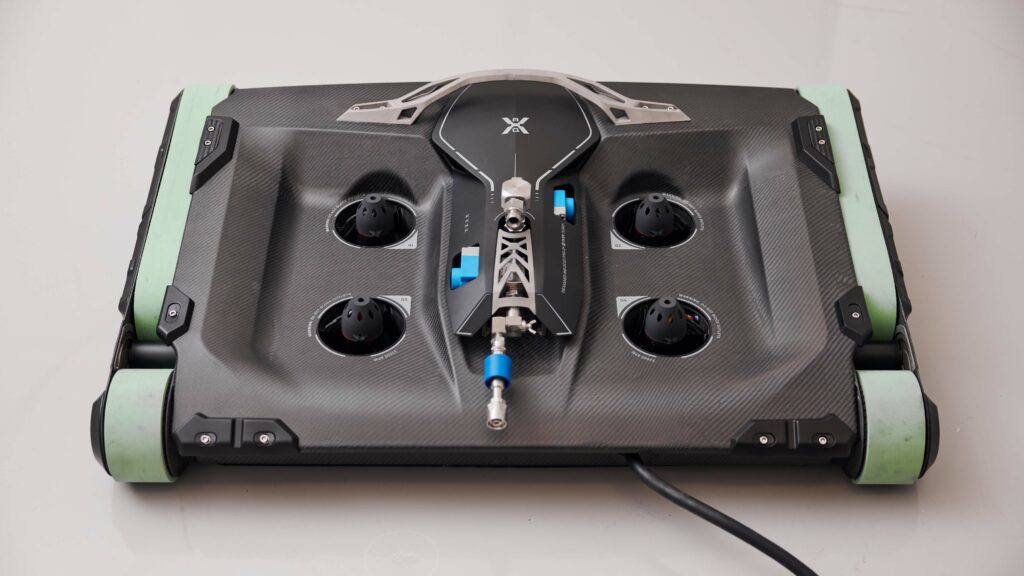
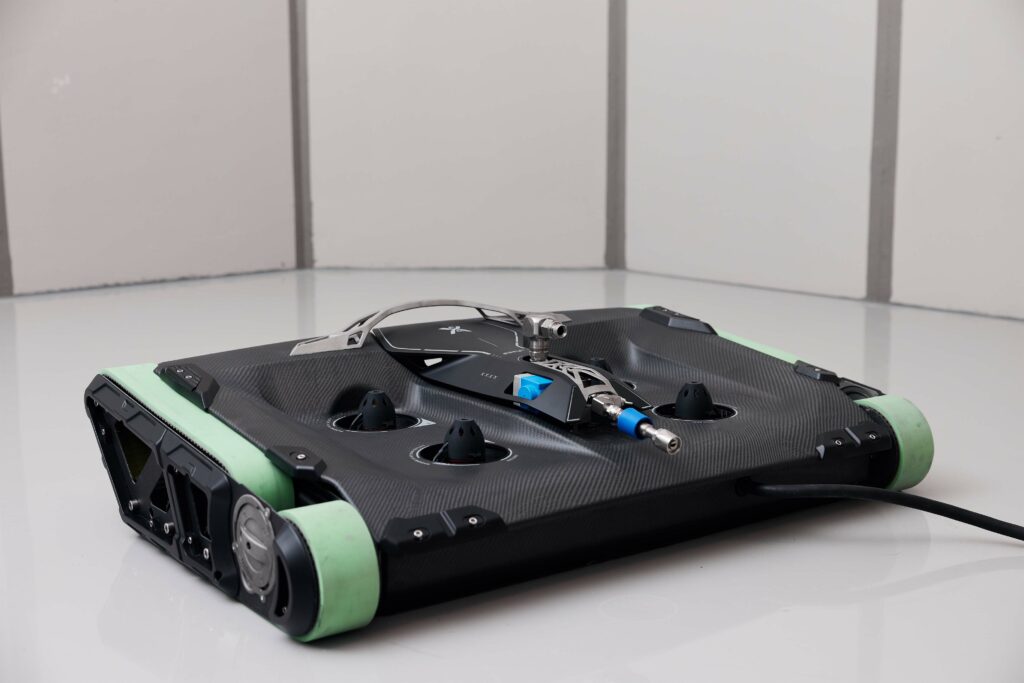
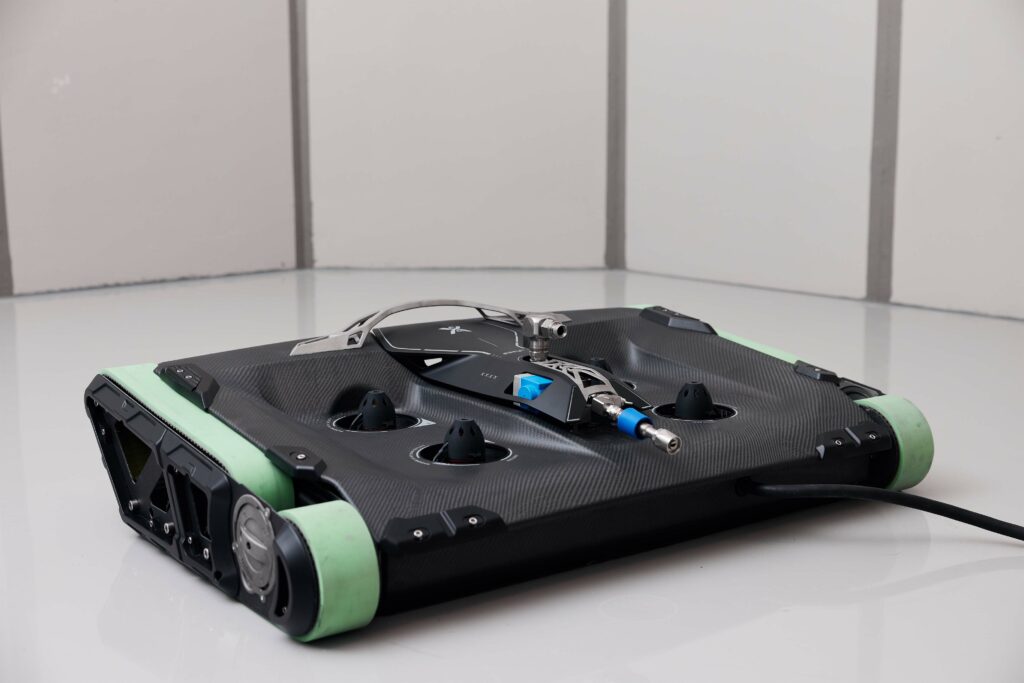
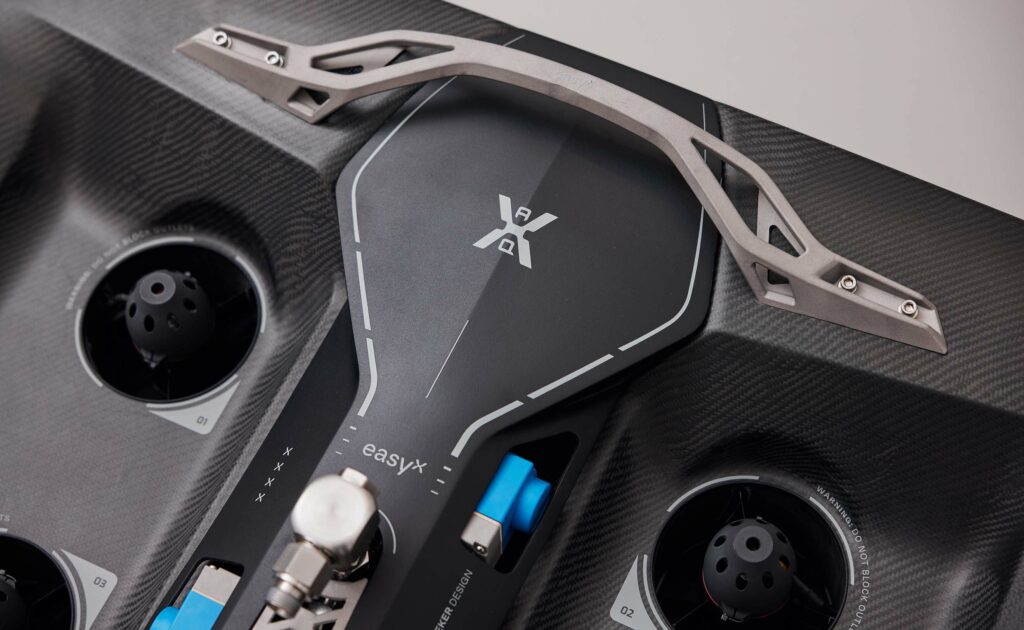
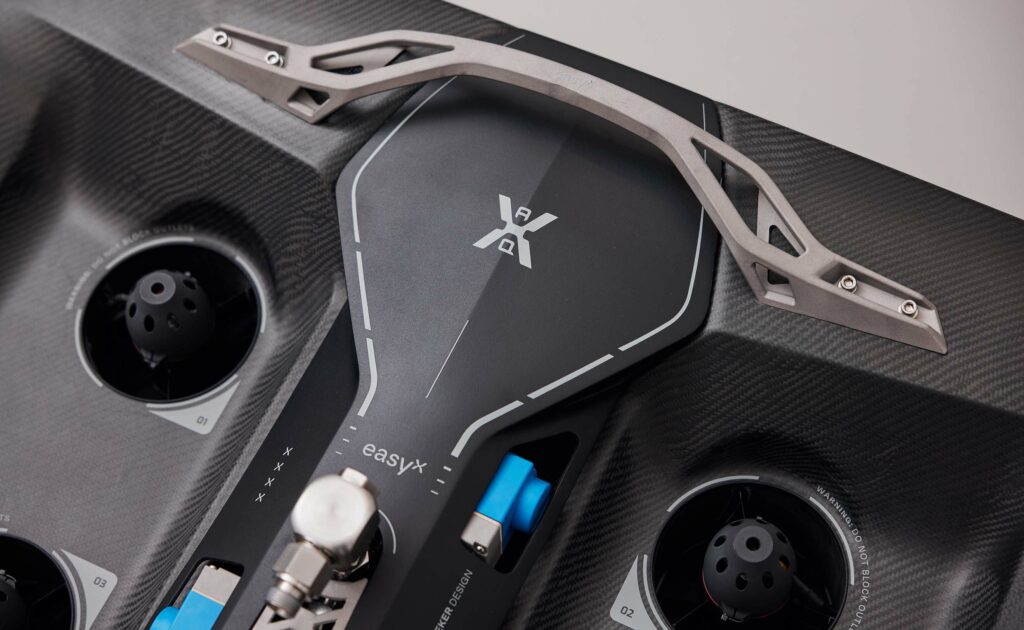
Prototype 2
When moving from tank to tank the robot must be decontaminated to prevent spread of bacteria and harmful organisms. The belt is lined with a special spongy and grippy material to provide enough friction. This material is quite fragile and difficult to decontaminate and therefore the belts must be changed frequently. An easy access tensioner mechanism was incorporated and made belt change without using any tools possible.
Further, the fishtank surface consist of a special urea-based compound. This surface can easily be damaged, and repairs are very costly. The xAQ has no protruding hard and sharp parts. Its hull has been fitted with rubberized bumper parts to protect the tank surface.
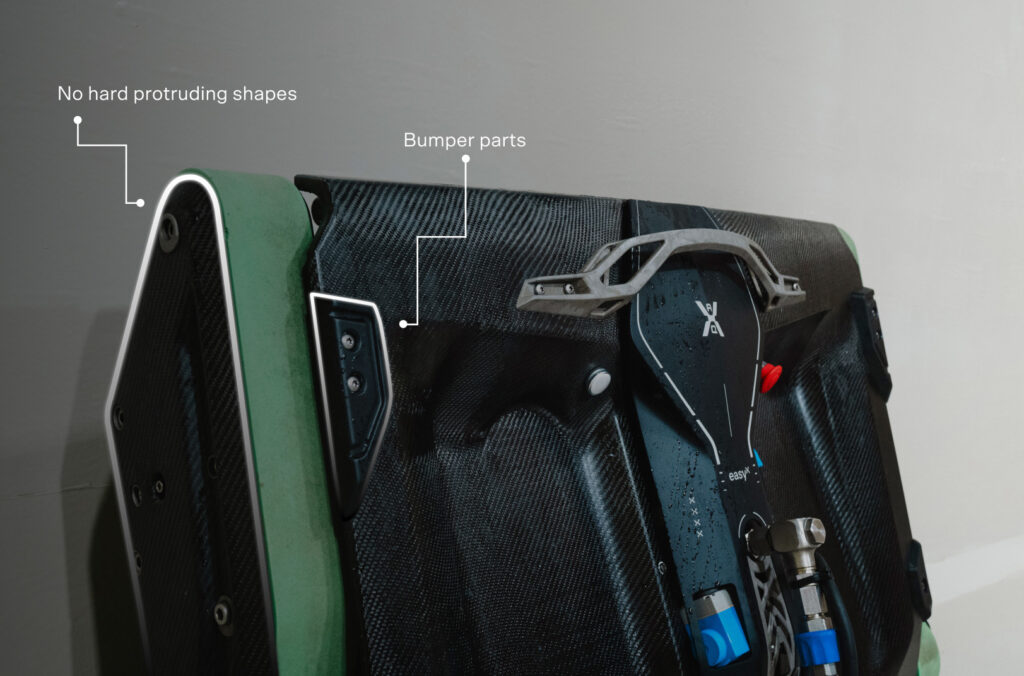
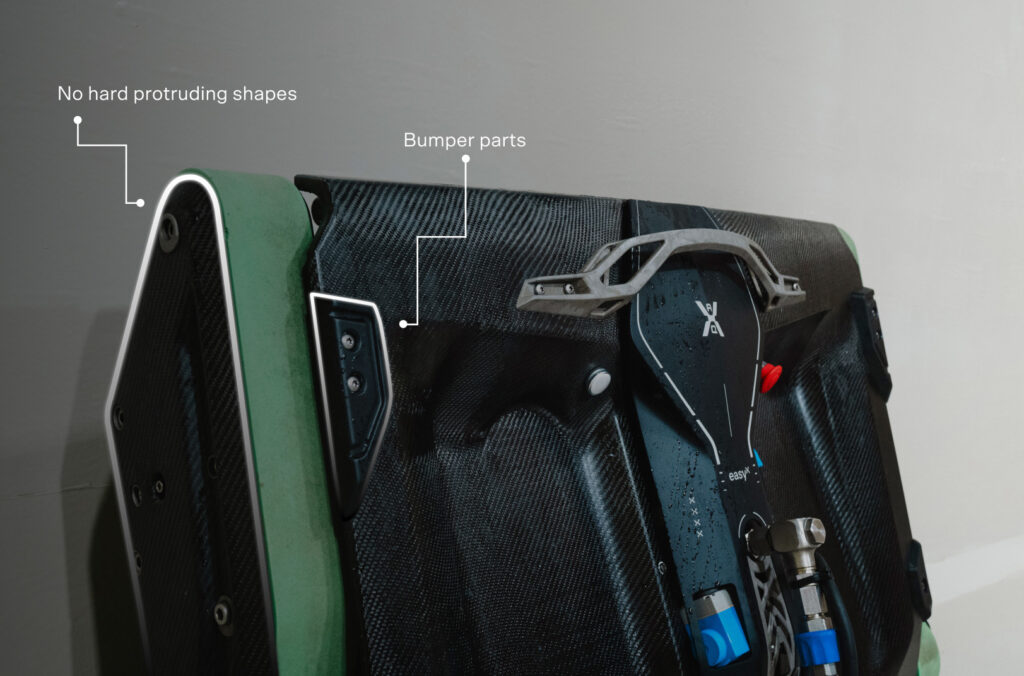
The total downforce created by the vacuum had to be raised from 150 to 600 kg and in turn the whole design had to be beefed up to withstand the higher load. This was made possible with several different measures: thicker carbon laminate wall thickness, sandwich construction in the hull laminate, transversal steel stiffeners inside the hull, more effective bonding between the hull parts, redesigned belt tensioner.


The design also had to be made a little more compact to more easily be carried through the standard sized manholes in the tanks. The vacuum effectiveness depends on the hulls distance from the fish tank surface. To find this sweet spot a height adjustment mechanism was incorporated in the new design. More thoughtful use of 3D printed stainless steel parts also meant reduction of traditional fasteners.











Status and next step
As of now EasyX is conducting pilot runs at several of the largest fish farming companies in Norway. The company is well underway in finding a working system for cost effective cleaning of these tanks. A long-awaited solution to this pain point in the fish farming industry! Next step on the development side of this project is to incorporate more automized systems towards full autonomy. We are looking forward to also applying our autonomy expertise in this project further along!



